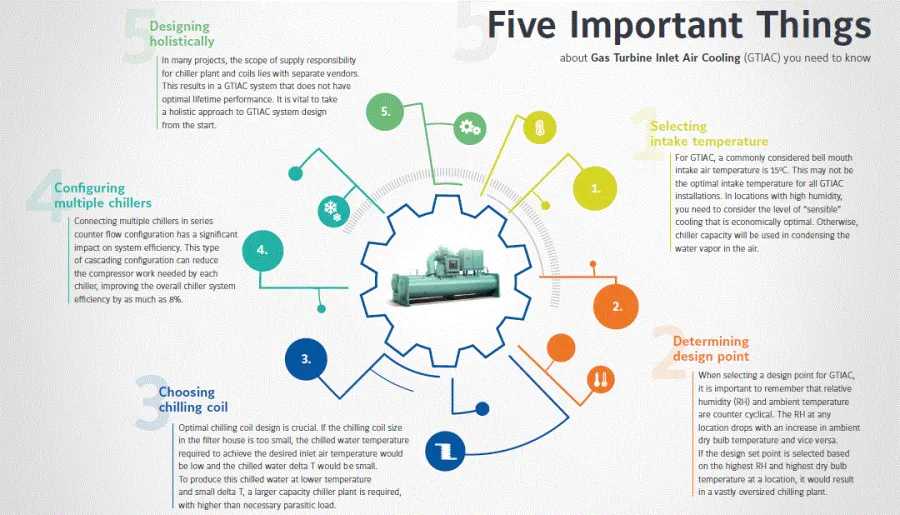
5 things about Gas Turbine Inlet Air Cooling (GTIAC) you need to know
GTIAC is a cost-effective optimised solution.
Today, there are various ways to enhance the power output of gas turbines. The most cost-effective means is Gas Turbine Inlet Air Cooling (GTIAC). This technology can increase a gas turbine generator’s output to produce 30%+ more electricity at a fraction of the cost of a new gas turbine generator.
The most consistently successful method of GTIAC is mechanical cooling. Based on proven water-chiller and heat-exchanger technologies, this method delivers the
cooling capacity, dependably and consistently to obtain optimal output from the gas turbine. Operating the turbine at the relatively constant conditions offered
by mechanical cooling can improve turbine life and lower maintenance costs.
Five important things about Gas Turbine Inlet Air Cooling (GTIAC) you need to know:
1. Selecting intake temperature
For GTIAC, a commonly considered bell mouth intake air temperature is 15oC. This may not be the optimal intake temperature for all GTIAC installations. In locations with high humidity, you need to consider the level of “sensible” cooling that is economically optimal. Otherwise, chiller capacity will be used in condensing the water vapor in the air.
2. Determining design point
When selecting a design point for GTIAC, it is important to remember that relative humidity (RH) and ambient temperature are counter cyclical. The RH at any location drops with an increase in ambient dry bulb temperature and vice versa. If the design set point is selected based on the highest RH and highest dry bulb temperature at a location, it would result in a vastly oversized chilling plant.
3. Choosing chilling coil
Optimal chilling coil design is crucial. If the chilling coil size in the filter house is too small, the chilled water temperature required to achieve the desired inlet air temperature would be low and the chilled water delta T would be small. To produce this chilled water at lower temperature and small delta T, a larger capacity chiller plant is required, with higher than necessary parasitic load.
4. Configuring multiple chillers
Connecting multiple chillers in series counter flow configuration has a significant impact on system efficiency. This type of cascading configuration can reduce
the compressor work needed by each chiller, improving the overall chiller system efficiency by as much as 8%.
5. Designing holistically
In many projects, the scope of supply responsibility for chiller plant and coils lies with separate vendors. This results in a GTIAC system that does not have optimal lifetime performance. It is vital to take a holistic approach to GTIAC system design from the start.