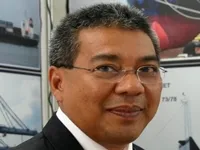
Reducing diesel power plant HFO bill
By Reducing diesel power plant HFO bill
The first half of 2012 saw fossil fuel prices skyrocketed to new highs. Heavy Fuel Oil ( HFO ) cSt180 went up to a ceiling of USD800 per ton.
60 – 70% of Thermal and Diesel Power Plant operating cost is fuel. A typical 60MW rated Base Load Diesel Power Plant (DPP) running at 85% Load Factor with a Specific Fuel Consumption ( SFC ) of 230 litres/MWHr, will consume 281.5Tons of HFO costing USD225,216 per day.
The operating fuel cost per 335 operating days year will be a whooping USD75.5Million generating 410GWHr of electricity. The fuel cost is USD0.184 per kWHr. Thermal and Diesel Power Plant operators were thus severely challenged to reduce its fuel and operating bill cost.
DPP remain a popular option to generate electricity for Base Load and Peak Load requirement. In circumstances, such as an island or remote region where the Peak Demand is below 100MW, DPP is the convenient and practical choice.
DPP can be rolled out from scratch within 9 - 15 months. A sea cable or on land high voltage transmission line with the mainland will otherwise be costly and less economic alternative. Geography, in this circumstance, is a key factor in the choice for a DPP.
In the lesser developed countries, where availability of extensive network of high voltage transmission lines are limited, DPPs very often are constructed to meet short to medium term power demand in their periphery regions. DPPs thus remain a choice for decentralised power generation. DPPs can be small but distributed.
It can be configured to about 100MW capacity. This is especially applicable for captive base load power generation for mines and industries in isolated interiors. Coal and gas fuel power plants remain economically suited for bigger than 100MW size generation capacity.
Base Load DPPs runs on Medium and or Slow Speed Diesel Engines. DPPs more often than not have multiple engines. A rated 60MW DPP can be configured with 4 units of Slow Speed 15MW Diesel Engines, 6 units of Medium Speed 10MW engines or 12 units of Medium Speed 5MW Diesel Engines depending on the flexibility for varying generation load requirement and for spinning reserves circumstances.
HFO is used for DPPs with Medium and Slow Speed Engines. HFO cSt180 , a residual grade oil from the crude oil refinery process, cost about 40% lower than High Speed Diesel fuel oil. HFO is relatively easily available and transportable.
HFO has impurities and a Purifier system is installed at the DPP to remove these impurities including engine damaging traces of water and hard catalytic fines ( silica and alumina ), and combustion impeding asphaltenes and etc.
These impurities including valuable agglomerated HFO, collective called as Sludge, are centrifuged out. The purified HFO is later fed into the Engines for safe combustion to generate electricity. Sludge is inherent in HFO. Typiclly 1 - 1.5% by volume of HFO is lost as sludge.
The Homogenizers is one proven solution to reduce the fuel consumption in DPPs. The Homogenizer is a HFO fuel treatment machine. Typically, a Homogenizer is installed before the Separators ( Purifiers ) system. Refer photo enclosed.
The raw HFO is first treated and homogenised. The HFO long chain hydrocarbon particles are sheared using the high speed rotor on stator mechanism. The HFO particles, average 70µ size, are consequently reduced and homogenised to 3µ size.
Except for the harmful water and catalytic fines, the homogenised HFO will pass through the centrifuge. This homogenisation process thus recovers the valuable and burnable fuel oil content of the HFO sludge.
Up to 80% of the ‘ sludge ’, which otherwise would have been lost as waste, is recovered. The homogenizer unit is hence referred to as Sludge Reduction unit.
DPPs usually install separate units at the Booster Module before the Engines. These homogenizer units, by virtue of the fine 3µ particle sizes, facilitate efficient atomisation and hence combustion.
Engine components life become extended consequently and above all traces of unburned HFO hydrocarbon, particulate matters and soot, which increases smoke opacity ( visibility ) will be significantly reduced. This makes DPP more environmentally acceptable and compliance.
For a rated 60MW DPP, the combined value of fuel oil ( HFO ) recovery is USD0.84Million per year, equivalent to an estimated 1% cost saving in fuel bill. Please refer to the graph enclosed for overall comparison.
Marizan Nor Basirun, Managing Director, S.I.T Schiffs-&Industrie Technik (M) SB